Safety Audit
What Is a Safety Audit?
A safety audit is a careful, structured process to determine how your workplace’s activities and environments impact your employees’ health and safety. Its main goal is to ensure that you are compliant with key safety regulations, such as those set out by the Occupational Safety and Health Administration (OSHA). Safety audits also are designed to see if your safety program is working across departments within your organization.
If your workers are not following safety protocols as outlined in your workplace safety program, a well-conducted safety audit should uncover these unsafe conditions and acts.
Because the goal of a safety audit is to assess whether your workplace safety program is effective and being followed, it is ideal for a third party to conduct your safety audit. The safety auditing team should be made up of multiple individuals, making it more likely that safety issues and lapses in judgment will be noticed.
Once an audit is completed, you have a grace period to adjust your safety program according to the results of the audit.
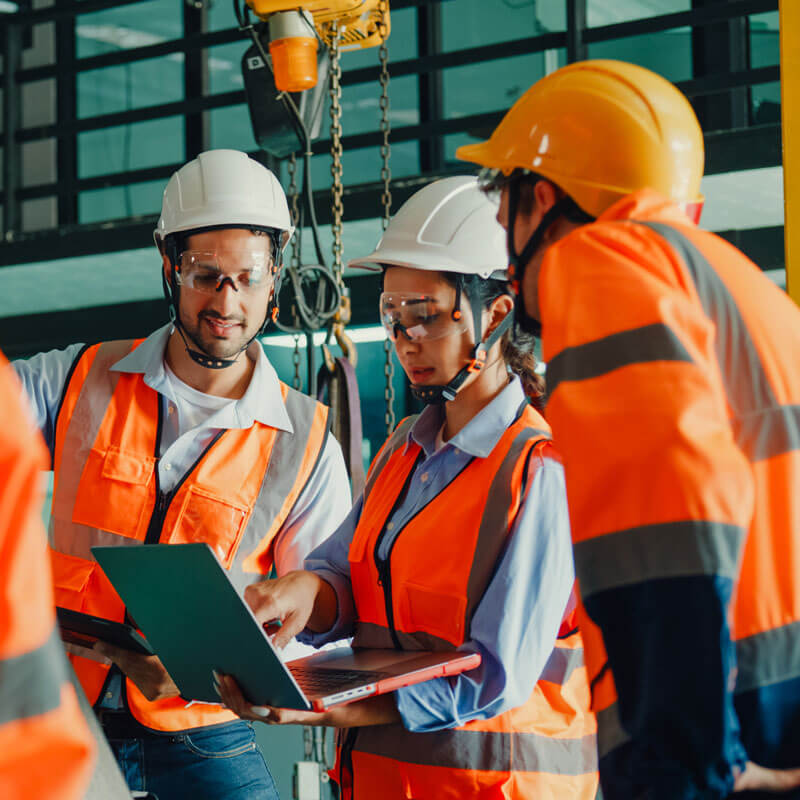
Why Perform a Safety Audit?
Safety audits typically aim to uncover:
- Risky employee behaviors, such as not wearing proper personal protective equipment (PPE)
- Unsafe working conditions that put worker health and safety at risk
- Areas of non-compliance with OSHA regulations
- Opportunities for improvement in your workplace safety program
If your workplace safety program is not comprehensive enough to address all worker risks, or if your workers are not properly following your safety program, a safety audit and inspection can uncover key safety hazards for you to address. This gives you an opportunity to address these potential issues before they become safety violations and hefty fines.
Top Benefits of Safety Audits
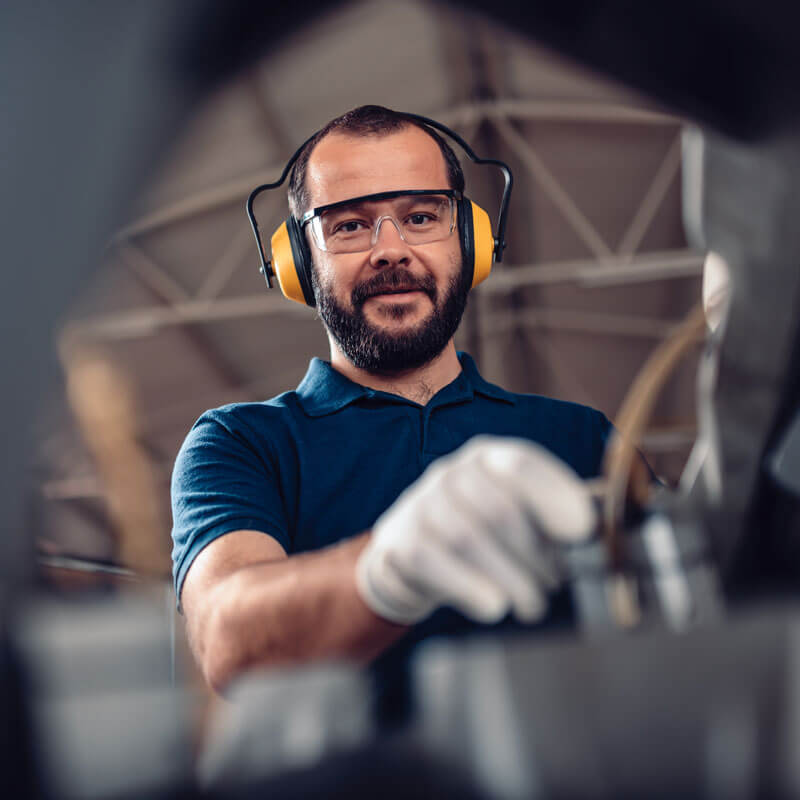
-
Not all workplace risks are obvious, and often the unknown risks are those that pose the greatest threat to company safety because they catch your workers off guard. A safety audit can help you identify both known and unknown risks, determine what level of threat they pose and what measures you can take to correct those risks to create a safer working environment.
-
Creating an effective safety culture starts with understanding where your strengths and weaknesses are now and taking steps to correct those weaknesses. Identifying the areas where your organization is already strong helps you understand what is working and how you can capitalize on your successes. Highlighting your organizational weaknesses allows you to take corrective action to reduce your workplace risks and build a more effective safety program.
-
A safety audit gives you concrete, actionable data you can use to make more informed decisions. If you do not know where your safety program stands now, you will just be making guesses about what changes need to be made. With a safety audit, you have the data right in front of you that allows you to make decisions that save lives, reduce accidents and improve efficiency among your workforce.
-
Shoring up your organization’s safety protocols and procedures requires money and resources. Having a safety audit with actionable data can help you prioritize which upgrades and changes to make first, and give your recommendations more weight with investors, leadership or your board of directors.
-
Staying compliant with rules and regulations is essential to your business’s long-term success. By identifying areas that need improvement, you are better able to create a comprehensive safety program that keeps you compliant with regulations. This allows you to avoid workplace accidents, OSHA violations and potentially costly OSHA fines.
What Is the Difference Between a Safety Audit and a Safety Inspection?
Both safety audits and safety inspections have as their end goal ensuring a healthier, safer working environment for your employees. They both also often involve a third party providing an unbiased view of your organization’s safety practices and procedures. But that is about where the similarities end.
Here are some main differences between safety audits and safety inspections.
- Scope of service: Safety inspections tend to have a more limited scope than safety audits. They are often a more targeted assessment to evaluate the safety of a specific area of your workplace and will often focus on one hazard or work task. Safety audits, on the other hand, are broader. They look at your organization’s safety plan as a whole and evaluate whether that plan is working — and where it can be improved.
- Frequency: Your organization should conduct a safety audit at least once per year, but more often if it is necessary. Safety inspections, on the other hand, may take place more frequently, sometimes once a week or more.
- Team makeup: Safety inspections typically are conducted by an organization’s internal teams, such as the safety department. This allows these inspections to be conducted frequently without incurring the hefty costs of hiring an outside team regularly. A safety audit, however, usually involves hiring an unbiased, outside team. This provides a broader look at your organization’s safety program and allows you to bring in a team with specialized skills and knowledge.
How to Conduct a Proper Safety Audit
To be effective in helping you improve workplace safety and reduce accidents, your safety audit must be conducted properly. Here’s how a proper safety audit should be conducted.
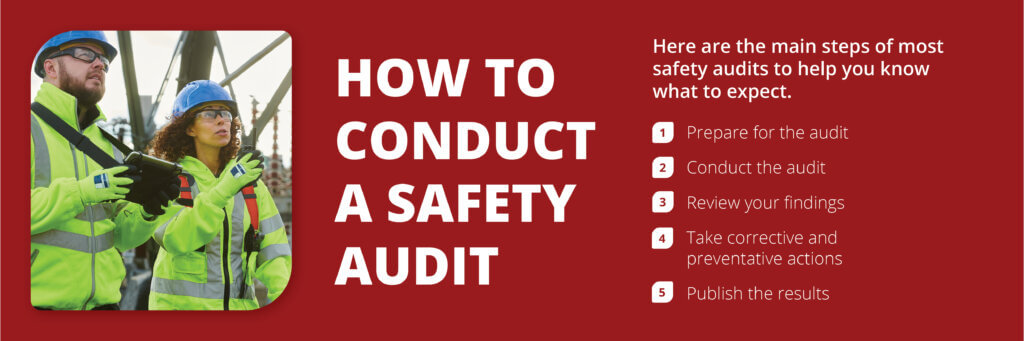
Planning
In this early phase, you will answer early questions regarding the audit and confirm information to help your audit run smoothly. When planning, you will likely:
- Inform your safety team, supervisors and managers that you will be conducting an audit. They will need to gather all the necessary documents and ensure their safety procedures are in place and operational. In order for the audit team to do their job quickly, all this information should be accessible by the time the audit begins.
- Review past audits and their recommendations for corrective actions, ensuring your organization is following them. Additionally, review any legal and training requirements relevant to your industry or specific areas of your company being audited.
- Determine the scope of your audit. Will it cover your organization’s whole safety plan, or just one aspect and how it is utilized in different departments?
- Choose your audit team. This could mean you hand-pick safety professionals outside your organization, or you partner with a dedicated safety auditing team.
- Decide on your audit timeline, including the start date of the audit, as well as all the days the audit team will spend auditing your company prior to the projected end date.
Conducting the Audit
Once all your preparatory work is complete, your audit team will conduct your safety audit. Most audits focus on:
- Employee knowledge of safety policies and procedures
- A review of your written program, comparing your safety program to federal requirements (including hazard control and identification, employee training and recordkeeping)
- Program roll-out and administration, checking how your program’s requirements are managed and implemented
- A review of documents and records to check for incomplete or missing records or documents
- An inspection of equipment and material to determine hazard control capabilities
- General walkthroughs of any areas involved in your audit
Your level of involvement with the safety audit will depend on the type and scope of the audit, as well as the needs and requirements of your safety auditing team.
Taking Corrective Actions
After the safety audit is completed, you will receive a report that outlines all the findings. This includes notes on what parts of your safety plan are working across your organization, and what parts are not.
For each deficiency found during the safety audit, it is essential to develop recommended actions to correct the problems. If you have workers in one department who are not correctly using PPE, for example, some potential corrective actions include:
- Scheduling additional training sessions with workers in that department
- Conducting periodic PPE “spot checks”
- Creating a warning and disciplinary system for workers who repeatedly violate PPE protocols
Be sure to involve supervisors and managers in the process of determining and planning corrective actions; they may have valuable ideas and insight that you may not think of. Assigning completion and review dates to all corrective action — and putting these dates in a centralized calendar — is key to making sure you consistently take steps to righting the wrongs pointed out in your safety audit.
Publishing the Results
The final step in your safety auditing process is to make the recommendations and findings available to all supervisors, managers and stakeholders. This makes sure everyone involved with your safety program can see which areas need improvements, which areas are successful and what actions you will take as an organization to improve your processes.
Frequently Asked Questions
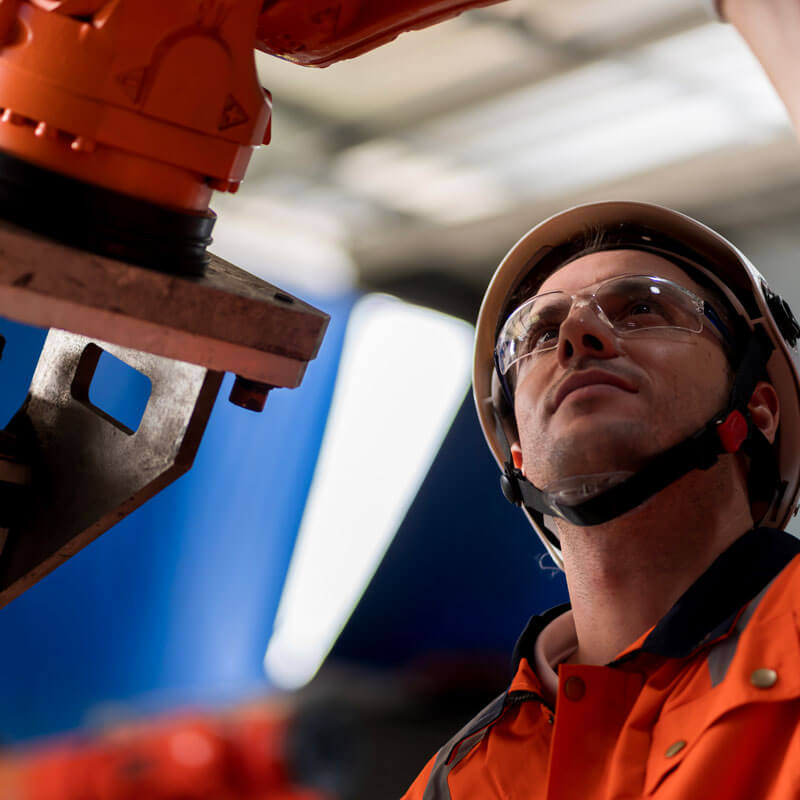
-
A safety audit is an in-depth evaluation of an organization’s safety policies and procedures, identifying hazards and outlining potential next steps to creating a healthier and safer workplace. These are typically conducted by neutral third parties with deep safety knowledge and experience, allowing them the broadest view of an organization’s overall safety procedures and plans.
-
Maintaining workplace health and safety is an ongoing process. Once you have developed and communicated a safety plan, it is important to continually ensure that plan is being followed, and to identify potential new hazards or weak spots in your safety plan. An audit shines a light on those areas where your organization needs some improvement, giving you actionable steps you can take to create a better safety culture.
-
Safety audits are not without their challenges. Things such as lack of resources, resistance to change or inadequate training could become roadblocks to conducting an effective safety audit.
-
While OSHA does not directly require safety audits in many industries, some of its standards do require organizations to evaluate their workplace and identify potential safety hazards. The organization states that routine safety audits are an important part of an effective safety program.
However, OSHA does require that employers take responsibility for accident prevention, and any workplace safety programs should include processes — including safety audits — that demonstrate they have preventative safety measures in place.